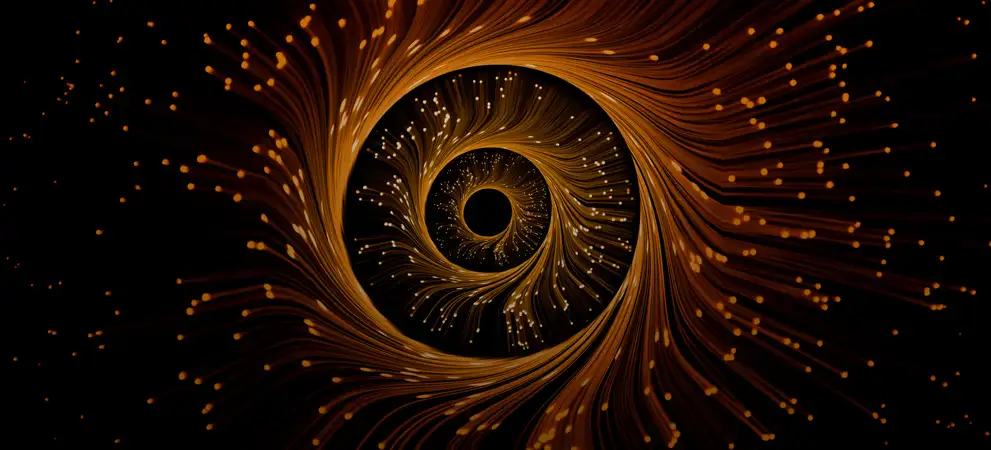
Product Realisation
Translating ideas into scalable, tested, production-ready designs
Transforming a concept into a tangible product is what product realisation is all about, whether the plan is for specialist, low-volume manufacturing or mass-produced consumer products – and everything in between.
The aim is to translate ideas into sustainable, robust, scalable, tested and approved designs – involving all aspects of research, design, development, testing and production along the way.
Supply chain management, for example, needs to include consideration of the long-term availability of components and materials, while design for assembly aims to reduce the number of components and minimise the number of assembly operations to optimise the manufacturing process.
The implementation of design for manufacturing principles at an early stage of development is critical to deliver a product to match a company’s business goals in a manageable and controlled timescale.
This could involve monitoring congestion as part of a smart traffic system to warn drivers which roads to avoid, for example, or analysing CCTV images as part of a security system and raising the alarm if a perimeter has been breached.
Real-world challenges
Key skills
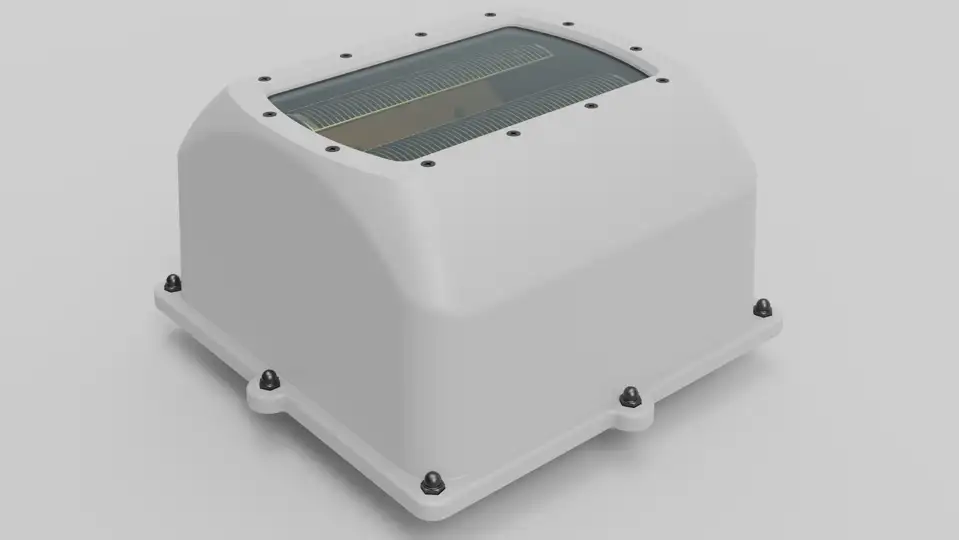
-
Mechanical design
Using the latest Creo design software.
-
Printed circuit board
Using either PADS or Altium for the layout of all types of complex digital, RF and high-speed designs.
-
New product introduction
Overall management of all aspects of product realisation for mechanical and electronic designs.
-
Design for manufacturing (DFM)
Products are designed with manufacturing considerations and restraints in mind to avoid iterations in later projects stages and optimise time to market. Includes looking at PCB layout and product CAD designs.
-
Supply chain management
Advising on the choice of best contract manufacturing services and customised part manufacturing vendors to match the business model and create the best partnerships for the future.
-
Design for purchasing
Complete bill of material analysis to avoid using parts close to obsolescence, prevent critical part shortages and understand the lead time ready for builds.
-
Design for process engineering
Product collaboration with the industrialisation and manufacturing teams to develop lean assembly steps for cost and time reductions.
-
Design for test
Product collaboration with the industrialisation and manufacturing teams to develop lean assembly steps for cost and time reductions.
-
Design for assembly
Implementation of required manufacturing and assembly processes, with corresponding work instructions.
-
Quality Management
Plextek have installed a Quality Management System certified to both ISO 9001:2015 & ISO 13485:2016, which gives a framework that can be tailored to match the requirements of every project in order to meet our clients’ expectations.
What sets us apart when it comes to product realisation?
The Plextek team has a track record of delivering complex technology solutions, using our expertise to take on a concept design and transform it to create a solution to match a client’s business goal. To achieve this, our offer includes:
- New product introduction (NPI)
- Design for manufacturing
- Understanding the whole supply chain
- Managing of projects from concept to end of life
- Research and innovation services
The tools we use to create best-in-class design include:
- Creo mechanical design package
- Pads/Altium PCB layout
- Option to work with the tools of your choice, such as SolidWorks